Parts in the Plastic Injection Molding Industry:
- Plastic Injection Moulds
- Screws
- Barrels
- Nozzle tips and nozzle bodies
- Side-action cores and cavity inserts
- Ejector Pins and sleeves
- Slides and lifters
- Bushings and guide pillars
Requirements for the parts:
- For high Wear resistance
- For high Fatigue strength
- For Reduced friction and adhesion
- For Corrosion resistance
Ion Nitriding Solutions:
Significantly increasing the surface hardness, wear (abrasive and adhesive) resistance and fatigue life of the tools, improving their lifespan and performance.
- Reducing the friction coefficient and the adhesion of the plastic material to the tools. Nitriding will also lower the friction for bushings and guide pillars.
- Increasing the corrosion resistance which is needed for certain additives and processing conditions.
Improving these parameters will save from downtime and maintenance costs.
Steel Grades Used:
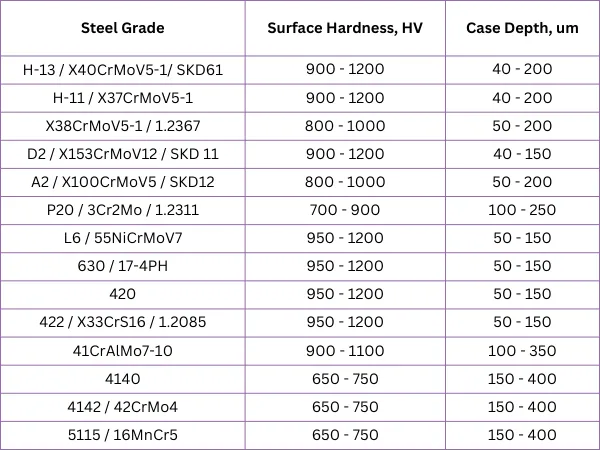
Hardness and depth values are recommended for the industry and exact values will depend on the nitriding process parameters.
This is not a full list of used steel grades
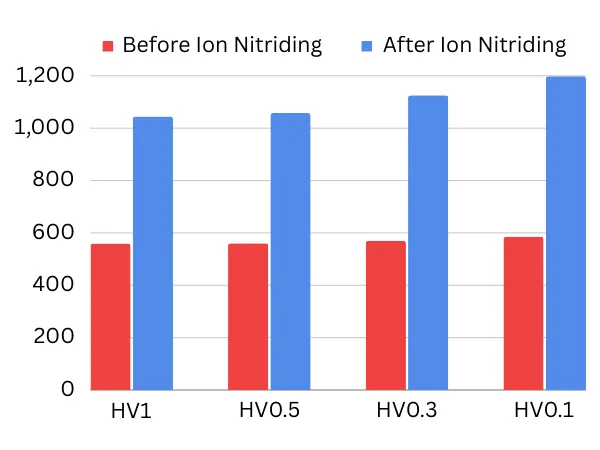
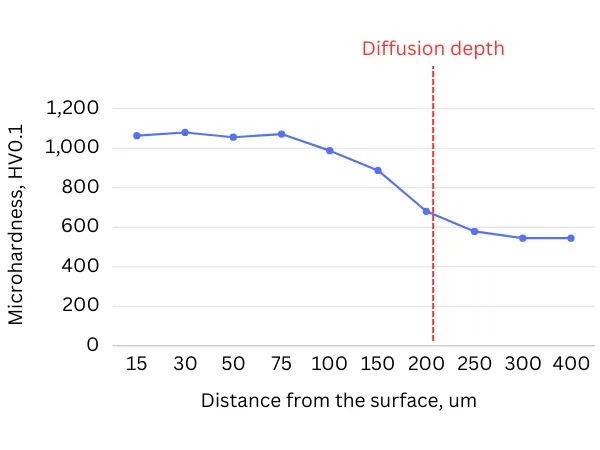
Example of H13 tool steel after Ion Nitriding - surface hardness and diffusion depth